Testing Capabilities
All analytical and testing compliance is performed by the NADCAP certified HPW in-house laboratory.
Thickness Testing
- X-Ray Fluorescent Analysis (XRF)
- Beta Backscatter Analysis
- Mechanical Inspection
Passivation Testing
- Water Immersion Test
- 24-hour Salt Spray Test
- Copper Sulfate Test
Adhesion Testing
- Bend Test
- Tape Test
- Heat Quench
- Chisel-Knife Test
Heat Cycle
- Adhesion
- Hydrogen Embrittlement Relief
- Hardness of Deposition
- Stress Relief
Solution Analysis
All process baths and outside analysis accepted
Solderability Testing
All process baths and outside analysis accepted
Gold and Silver Purity Analysis
As required per specification
Salt Spray Analysis
As required per specification
Tarnish Resistance Analysis
As required per specification
Porosity Testing
As required per specification
Electroless Nickel Phosphorous Composition Testing
As required per specification
Nitric Acid Testing
As required per specification
adhesion failure
What You Should Know About Metal Plating Adhesion Failure
There’s nothing worse than looking at a newly plated part with peeling or blistered plating. It is especially bad if you are ready to assemble and ship to your customer. It can be an even bigger problem if the adhesion failure is not discovered until after assembly. Non-adhesion is a common reason for rejection of plated hardware.
There can be a variety of reasons for adhesion failure. Many times the cause is insufficient cleaning before the plating process even begins. All plating processes start with several cleaning requirements; next is testing to verify the effectiveness of the cleaning. Only then can we progress to the activation process, and finally to the plating bath.
Another source for the problem can be delays between immersion into the various process baths. If the hardware is allowed to dry between process requirements, an oxide or passivation may begin to form on some base materials. Or, perhaps the delay is caused by poor electrical contact in the plating tank. These issues can lead to ultimate adhesion failure.
An additional cause of adhesion failure can be secondary processing. That is, testing or processes performed by an outside contractor that can degrade the plating and result in adhesion failure. Perhaps an environmental heat cycle or high humidity test, not provided for within the scope of specification, but required by an end-user. Or, maybe a soldering step using a temperature that adversely affects the plating adhesion. There are many different avenues that lead to a root cause of this failure.

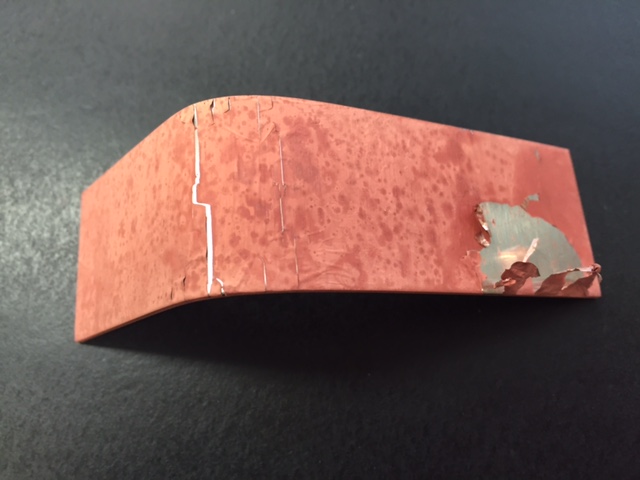
Conceivably, we now understand why the failure happened. What can be done to prevent adhesion failure from reoccurring? As the customer, an important first step is the use of an accredited plating house. Certification to one of the many ISO or Nadcap programs is an essential starting point. Holding the accreditation provides assurance that the plating facility is operated at the highest quality level; that all baths are free of contaminants and at prime operating parameters.
Another important step is communication, or flow-down, from the customer and within Hudson Plating Works. We perform a thorough statement-of-work for each job. During this procedure all questions are addressed by all departments. The Quality Department is charged with bringing together processors, preparation staff, laboratory staff, and sales staff. Together with input from the customer, all questions are adequately addressed. Only then is the job released for incoming inspections, processing, testing and finally packaging and shipping.
It’s important to remember that providing as much information as possible regarding the plating requirements is invaluable. If the hardware is a new design or an exotic material, or maybe selective plating, its always a good idea to run a first article. A little R & D work can be crucial. Oh, and again, always use an accredited plater. That’s Hudson Plating Works!